KILWELL FIBRETUBE - TOUGHER THAN THE REST
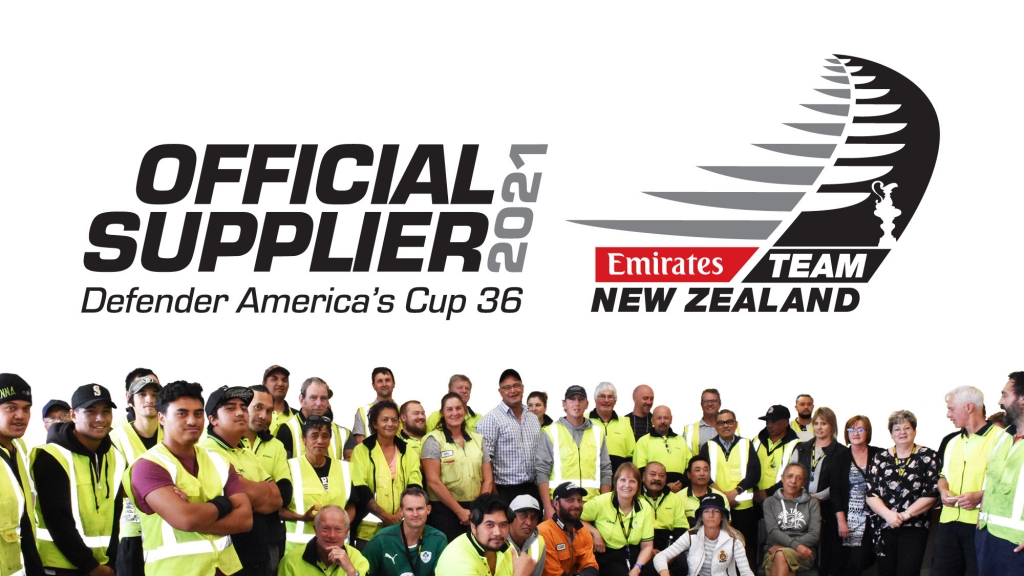
Read Kilwell Fibretube and you might be forgiven for thinking of fishing rods. They’ve been making them in New Zealand since 1968. But these days, fishing rod blanks make up only 3-4% of Kilwell Fibretube’s total production.
They’re now a world leader in composite innovation and make paddle shafts, rowing oar shafts, masts, booms, prods and spinnaker poles, stern tubes, outriggers, and telescopic pole sets.
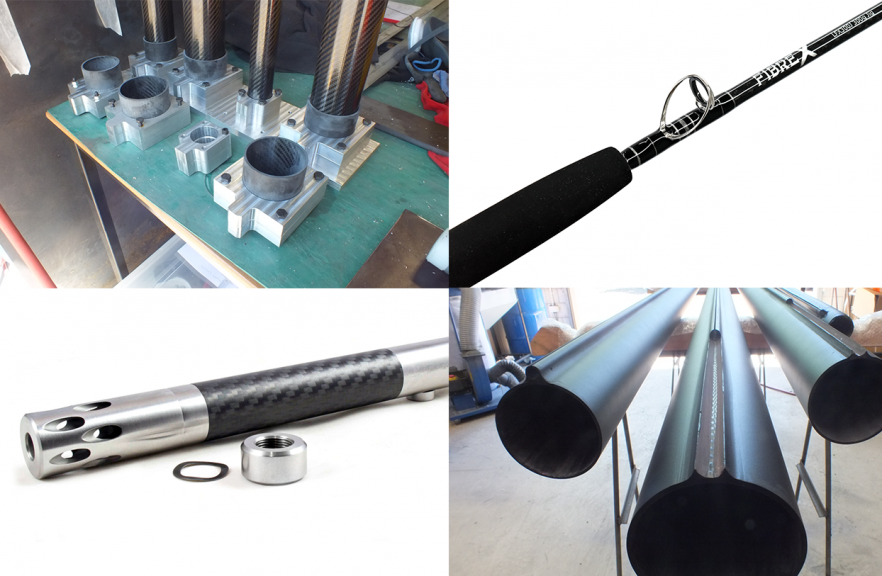
Some of the many products Kilwell specialise in, including rifle barrels, masts, and fishing rods
In 2018 the company was named the Rotorua Business Awards Winner in the Innovation & Disruption Category and was also the proud recipient of the Judges Acknowledgement for Excellence Award.
Small, privately owned and based in Rotorua, Kilwell is currently putting the final touches on Te Ahi Tupua, aka “Hemo”, the world’s largest 3D sculpture.
They’re also supporting Emirates Team New Zealand. Literally.
Kilwell’s carbon fibre and composite tubes are being used as a sort of temporary skeleton for the yacht. Chief Executive Craig Wilson explains:
“When they build the hull, they put tubes on the inside to hold everything in place to give it structure and then once it’s all made they take them out. And the big tube that holds the mast in place when it comes down and sits inside the boat, that’s ours too.”
Wilson says Kilwell’s new status as official supplier to Emirates Team New Zealand is helping to change the way the company is perceived.
“A lot of people in New Zealand still only know us for making fishing rods. So it’s really good for us to be able to go out and say we’re also making tubes for Emirates Team New Zealand. It’s helped get our name out there and opened people’s eyes about who we are and what we do. Emirates Team New Zealand only deals with the very best so it’s a great fit for us.”
It was a deal that Kilwell was determined to clinch.
“We’d made a few products for them in past campaigns but this year we made a concerted effort and went up and pitched to them what we’re doing and how we’re changing. We really wanted to be involved. Because the rules have changed so much on how and what they’re allowed to make, we weren’t really sure whether we had a chance, but it turned out the way we produce our tubes worked well with their design requirements. Some of the things they make are not allowed to be cured using an autoclave (a giant pressurised oven), but we use a mandrel roll process for manufacturing - essentially our products are cooked in an oven all strapped up. Recently a company in the US took tubes from all over the world to get tested and found ours came out 30% stronger compared to the autoclave ones - that debunked a few myths and worked out well in our favour.”
With 85% of its composite tubing design and manufacture exported worldwide, Wilson says the team is very proud to be involved.
“Our guys on the factory floor really like it when they know who they’re making products for and how it’s going to be used. Instead of making something that goes on a ship or a plane for export, this is something that’s actually going to be used in New Zealand for New Zealand. It brings a real sense of pride for them.”
And although the work for Emirates Team New Zealand can be challenging, Wilson says Kilwell is taking it all in its stride.
“Some people might find it challenging, but we see it as an opportunity to learn and work with new products, materials and designs. We’ve had to make a few changes in that some of the materials they wanted us to use were a bit different. But that’s good, it’s made us learn and adapt, and got us out of our comfort zone.